SATO Success with RFID: Precision in Every Byte: SATO’s RFID Revolution in Computer Spare Parts
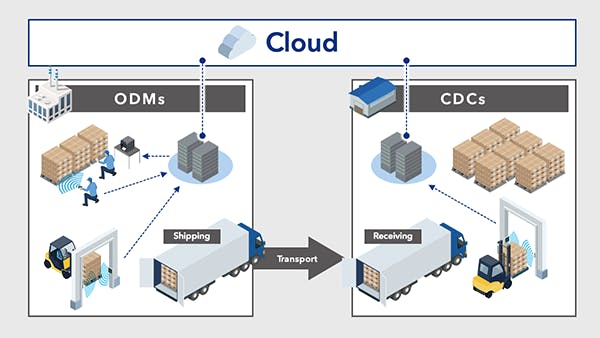
A global technology leader involved in the design, production and distribution of diverse computing and IT products like PCs, laptops, servers, storage devices, networking gear and peripherals, this customer required effective global parts tracking to streamline operations for rapid customer response. Implementing RFID technology provided real-time visibility and management of parts to allow the company to seamlessly track the movement and status of each component across its global network. In essence, RFID integration was a strategic asset, optimizing processes and contributing to the company’s success in the fast-paced world of technology.
Business Challenges
The company is running a spare parts business worth approximately $4 billion through its global channel business and sought to enhance the efficiency of its inventory handling operations across the supply chain. Specifically targeting its service parts business, including ODMs (original design manufacturing) and CDCs (central distribution center), the company aimed to implement RFID technology to replace existing barcode practices for inventory ID and tracking in global management of repair parts. The primary objectives were to streamline inventory management, optimize reporting functions, reduce costs by minimizing excess inventory in the supply chain, and enhance customer satisfaction by consistently meeting service-level agreement (SLA) requirements.
Solution
SATO delivered a customized turnkey solution in collaboration with key partners, backed by a dedicated 24/7/365 call center. The fully integrated SATO Cloud RFID System, which includes printers, labels, software, RFID fixed and mobile readers, RFID cloud software, gateways and software, cloud hosting, service and support, established seamless communication with the customer's Original Design Manufacturers (ODMs) and Central Distribution Centers (CDCs). This comprehensive system facilitated efficient coordination and data exchange between various supply chain components.
The solution enhanced the ODM Outbound and CDC Inbound processes by implementing several key steps. These included introducing a user-friendly browser interface for EPC (electronic product code) requests, applying RFID labels to parts, establishing links with product attributes, validating pallet contents using RFID mobile scanners, automating RFID reading during truck loading and inbound processes, employing RFID mobile scanners for efficient discrepancy resolution, and providing a browser interface for accessing item-level part data during outbound and inbound shipments.
Results
- Decreased costs – reduced excess inventory, lessened workload
- Increased productivity – faster, more efficient business processes (inbound, outbound, cycle counting, etc.)
- Increased customer satisfaction – reduced out of stocks, better inventory visibility/accuracy
- Increased revenue – better support for omnichannel strategies
Resources
Resources to help you explore, operate and maintain your SATO printer.