SATO Success with RFID: Using RAIN RFID to Manage Reverse Logistics of Orthopedic Implants Loan Kits
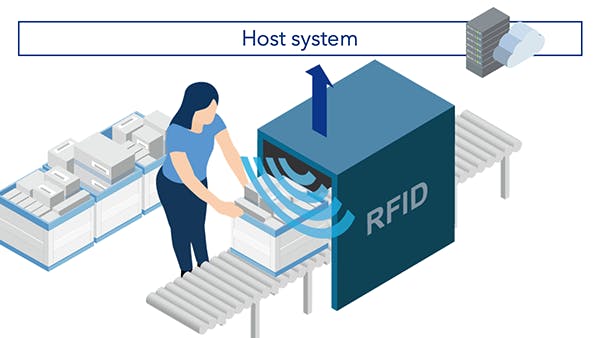
In the realm of orthopedic implant management, establishing visibility throughout the supply chain is imperative. This encompasses the meticulous tracking of items from the factory to distribution centers and onward to hospitals. The cyclical nature of this process involves the return of unused items to the distribution center for re-stocking, which are later sent back to the hospital. Efficiently and accurately managing this process is the key to implant loan kits management.
Business Challenges
The customer, a leading orthopedic implants manufacturer operating worldwide using RFID across 10 global sites, sought to boost efficiency in its distribution centers. It faced common challenges in orthopedic logistics: safety, traceability, labor shortages, and supply chain optimization. Individual barcode scan loan kits emerged as a bottleneck, resulting in prolonged periods where items were out of inventory. This could potentially lead to unnecessary stock orders and the mobilization of staff who could be allocated to more value-added tasks.
Specific challenges revolved around the time constraints for inspecting a kit upon return, reconciling items mixed in different boxes and kits and ensuring a speedy replenishment of a kit before being shipped to the next customer. The overreliance on manual labor introduced risks of human error, particularly in complex processes sorting out mixed items or during night shifts when attention to detail decreases.
Solution
SATO designed a smart solution to simplify the movement of loan kits in the customer's distribution network, making every step more efficient. SATO began source tagging UHF RFID tags to items and loan kits right in the factory. Once prepared, these items were logged with detailed product info in the ERP system before being sent to distribution centers.
When the kits reach hospitals, only 10 percent of devices are actually used. The return process for the remaining 90 percent to the manufacturers' distribution center would be greatly streamlined, with kits returned for restocking with a semi-automated outgoing shipment process.
Before SATO's solution, manual scanning of kits at distribution centers took up to 20 minutes per kit (three to four boxes per kit) or five minutes per box, which was a significant hurdle. SATO streamlined this process by introducing RFID tunnel readers, cutting scanning time dramatically to a mere eight seconds per box. The RFID tunnel read multiple tags simultaneously, making the process as simple as passing the crate through a gate.
In conclusion, SATO's RFID solution not only simplified the loan kit circulation but also brought a new level of speed and accuracy to each incoming and outgoing shipment process, greatly improving operational efficiency.
Results
- Decreased time of loan kit inventory
- Timely and accurate shipping/dispatch
- Easy management of inventory and stock flow
- Time and cost savings across the supply chain
Resources
Resources to help you explore, operate and maintain your SATO printer.